Automotive light-weighting is a long-term trend because it reduces emissions and fuel consumption, and it increases vehicle range and performance.
Carbon neutrality is a new key driver in our industry and addressing the complex challenges around sustainability will contribute to cars of the future.
One critical topics is how to develop lightweight vehicle safer, quicker.
Cost saving through light weight solutions is also predominate in the increase of usage of polypropylene compounds.
Sumika polymer compounds Europe address an answer to those industry’s need by full supporting with cutting-edge CAE toll solutions.
INTRODUCTION
SUPPORTING INDUSTRY CHALLENGES
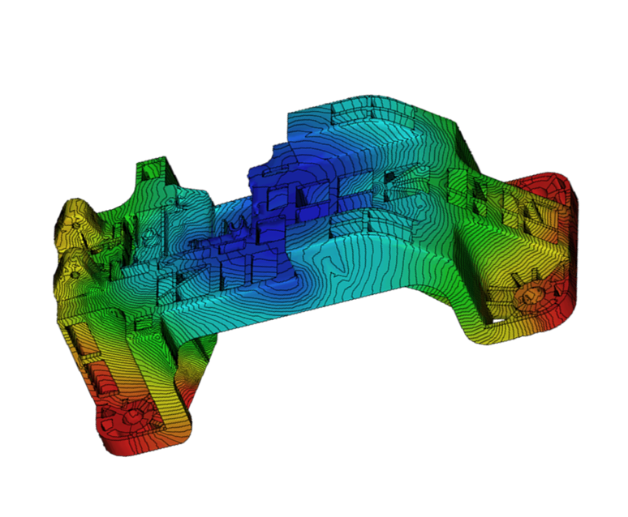
Automotive light-weighting is a long-term trend because it reduces emissions and fuel consumption, and it increases vehicle range and performance.
Carbon neutrality is a new key driver in our industry and addressing the complex challenges around sustainability will contribute to cars of the future.
One critical topics is how to develop lightweight vehicle safer, quicker.
Cost saving through light weight solutions is also predominate in the increase of usage of polypropylene compounds.
Sumika polymer compounds Europe address an answer to those industry’s need by full supporting with cutting-edge CAE toll solutions.
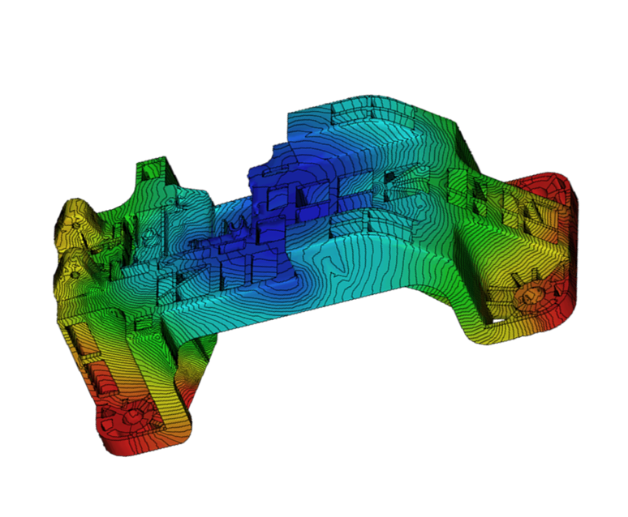
OUR ADDED VALUE
ENHANCING YOUR COMPETITIVE EDGE
In an era where innovation and efficiency are paramount, our CAE solutions offer a unique advantage to businesses across various industries. Our team of experts collaborates closely with clients to identify specific pain points and develop tailored CAE strategies. We believe in delivering tangible results that enhance your competitive edge. From streamlining engineering processes to improving product performance, our CAE solutions are a catalyst for your success. Explore how we can elevate your business to new heights.
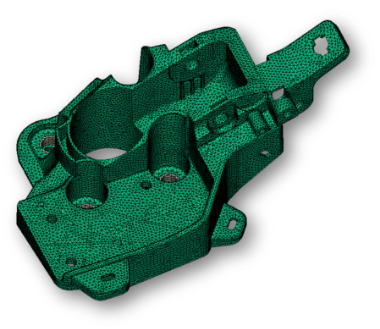
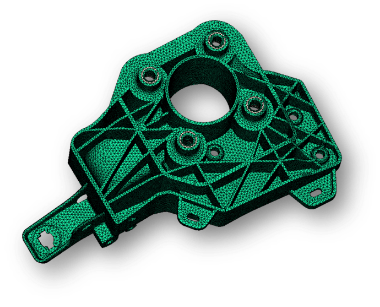
In an era where innovation and efficiency are paramount, our CAE solutions offer a unique advantage to businesses across various industries. Our team of experts collaborates closely with clients to identify specific pain points and develop tailored CAE strategies. We believe in delivering tangible results that enhance your competitive edge. From streamlining engineering processes to improving product performance, our CAE solutions are a catalyst for your success. Explore how we can elevate your business to new heights.
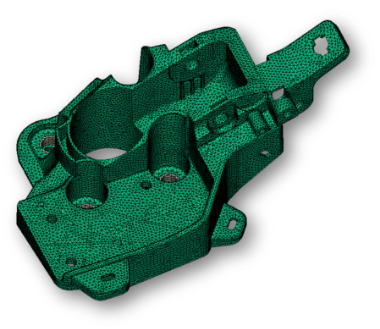
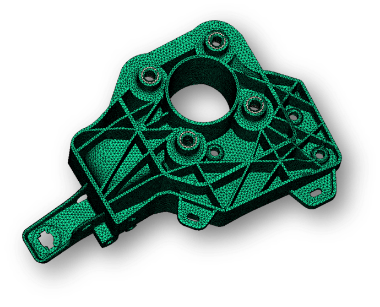
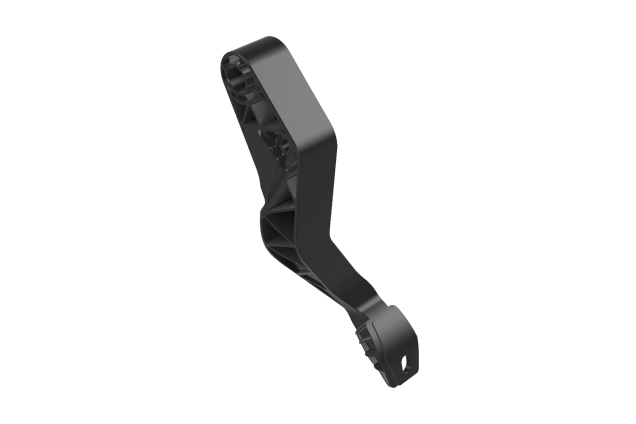
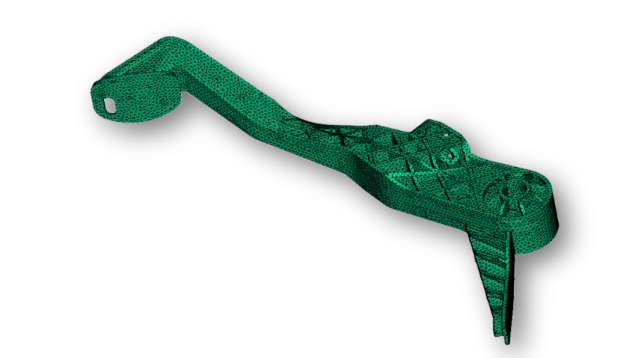
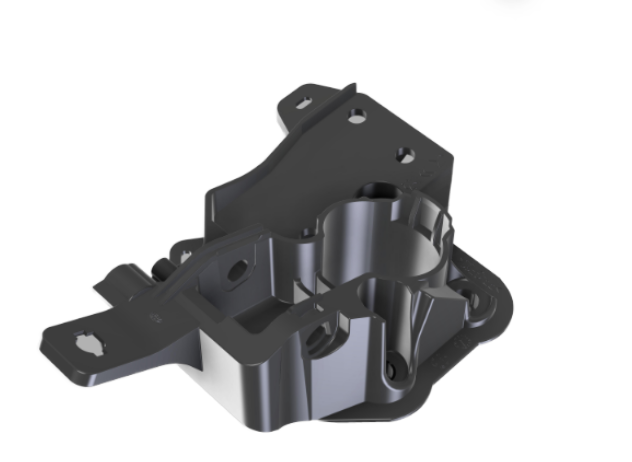
TAILORED SUPPORT FOR YOUR NEEDS
Case 1
You Own Digimat RP / FEA
Owned by You
Sumika Material Card
DIGIMAT MX
DIGIMAT RP
Customer’s Own FEA Software
Case 2
You Do Not Have Digimat RP
Sumika Material Card
DIGIMAT MX
Sumika Offers a DIGIMAT RP Floating
License with Full Training
(Free of Charge)
Customer’s Own FEA Software
Case 3
You Do Not Have FEA Support
Sumika Offers Its Own FEA Expertise Using
DIGIMAT RP and FEA Solutions
Customer Receives Full Results from Sumika
DIGIMAT TOOL
UNLOCKING ADVANCED MATERIAL MODELING
Digimat empowers engineers to analyze composite materials at both micro and macro scales. It predicts material behavior and calculates mechanical, thermal, and electrical properties for use in finite element analyses.
Typically, engineers begin by gathering material information and orientation data from tools like Moldflow, 3D-Sigma, Moldex3D, Simpoe, or other injection molding simulation solutions for molded materials. Digimat-MAP calculates residual stresses and temperature for each mesh element during the injection molding process, defining an ideal FEA structural mesh. Users can then seamlessly transition to FEA solvers like MSC Nastran or Marc, or any solver with a direct interface. Alternatively, they can use Digimat MF, MX, and FE to explore composite test data and assess the potential of more promising materials.
This approach allows users to understand the intricate relationship between part geometry, material flow during manufacturing, fiber orientation, and how these factors impact the final mechanical behavior of the component.
SUMIKA MATERIAL CARD
INJECTION SIMULATION
PRECISION IN PRODUCTION
Injection molding is a widely used manufacturing process, and achieving precision in production is essential for product quality and cost-effectiveness. At Sumika Polymer Compounds, we understand the critical importance of this process, and that’s why we provide a dedicated team of experts to support your injection simulation needs.
Our dedicated team offers several options for leveraging the results of these simulations. Clients can seamlessly transition to FEA solvers like MSC Nastran or Marc, or any solver with a direct interface, with confidence in the accuracy of our simulations. Alternatively, they can explore other possibilities using Digimat MF, MX, and FE to assess composite test data and evaluate the potential of more promising materials.
Our Digimat-MAP software calculates residual stresses and temperature for each mesh element during the injection molding process and defines an ideal FEA structural mesh. This precise approach ensures that your simulations are tailored to your unique production requirements.
Our dedicated team offers several options for leveraging the results of these simulations. Clients can seamlessly transition to FEA solvers like MSC Nastran or Marc, or any solver with a direct interface, with confidence in the accuracy of our simulations. Alternatively, they can explore other possibilities using Digimat MF, MX, and FE to assess composite test data and evaluate the potential of more promising materials.
With our dedicated team’s support, clients gain a holistic view of the entire production process, considering factors like part geometry, material flow during manufacturing, fiber orientation, and their collective impact on the final mechanical behavior of the component.
This collaborative approach not only reduces costs but also accelerates time-to-market, allowing you to deliver superior products to your customers.
At Sumika Polymer Compounds, we believe in the power of teamwork, and our dedicated experts are here to ensure precision in your production processes through injection simulation.